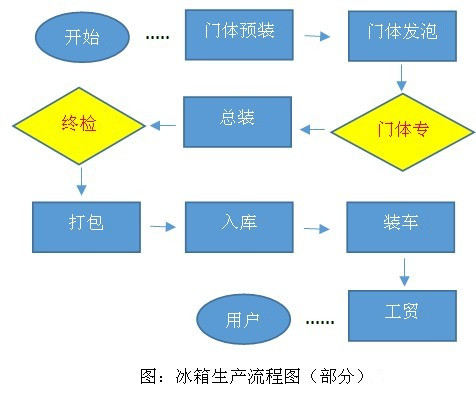
测量系统分析(Measurement Systems Analysis , MSA),即对测量数据的系统(人、机、料、法、环、量具)进行评估,其目的是保证测量过程输出的数据是真实可靠的。而正确的测量,或者说真实的数据永远是质量改进的第一步,为此,进行测量系统分析就成了企业实现连续质量改进的必经之路。
根据数据的类型,测量系统分析可分为计量(连续型)测量系统分析和计数型(离散型)测量系统分析,下面我们根据一个例子来讨论一下计数型测量系统分析在改善项目中我们经常会犯的一个错误。
小张是某冰箱企业2013年度精益六西格玛项目团队的项目组长。根据事业部的战略他承接了“降低冰箱门体外观不良损失”的市场项目,项目目前刚进入M阶段,根据项目的程序,小张针对门体的检验站(如图)组织了一次测量系统分析,结果显示门体专(全检)及终检(全检)的测量结果所有的一致性都是100%,说明测量系统是可靠的。既然这样,那按理说就可以进行下一步的分析了。
针对以上的结果,身为该项目的咨询师我问了小张以下两个问题:
1.既然测量系统是100%合格的,那么按理说门体不良品应该是不会流出厂外?
2.既然不良品不会流出厂外,那么直接从市场运输环节下手是不是就能最简单有效的降低市场的不良损失?
看着小张不置可否的表情我觉得问题并没有那么简单。带着刚才的问题,我们一起深入到流程了解了具体的情况:
⊙ 从终检日常的不良记录分析门体的平均不合格率为3.2%,经过对不良件实际鉴定分析发现,门体的不良主要由门体发泡本身造成的,这时问题来了:门体不良应该在门体专检的站点就检查出来的,为何会流到总装工序?
⊙在总装打包之后,质量部通常会定期的组织冰箱的开箱验货,根据记录得知,开箱验货的门体不合格率为1.8%,问题又来了:既然终检的测量系统一致性是100%,那么为什么开箱验货的时候还会发现这么多不良?
围绕以上的问题我们重新安排了一次测量系统分析,分析的步骤改为现场的模拟检验,即在正常的生产过程中设置相应的不良(沿用之前不良件),结果发现门体专验及终检的有效性为75%和78%。
到目前为止其实问题就变得明确了,该流程门体的两个检验站点的测量系统是不合格的,接下来只要找出两次测量结果之间的差异,问题就解决了,通常情况我们会思考:在进行MSA的时候,检验的环境是否发生了变化?检验人员有代表性吗?专门组织的MSA与实际的检验习惯(态度)是否不一致?测量工具有覆盖性?检验方法保持一致性吗?故障设置合理?等等…。
六西格玛是以数据为基础。如果我们能从数据本身发现矛盾、以矛盾激发问题并解决,那么就会具有更好的针对性。
声明:制造中国文章---属冠卓咨询内部专家原创内容,代表个人观点,授权于冠卓咨询网站使用;如需转载请保留原意并注明来源:冠卓咨询。请尊重原创!